What is Porosity in Welding: Ideal Practices for Avoiding Porous Welds
What is Porosity in Welding: Ideal Practices for Avoiding Porous Welds
Blog Article
The Science Behind Porosity: A Comprehensive Guide for Welders and Fabricators
Recognizing the complex systems behind porosity in welding is important for welders and producers striving for impressive workmanship. As metalworkers explore the depths of this phenomenon, they reveal a globe governed by numerous elements that influence the formation of these tiny gaps within welds. From the structure of the base materials to the ins and outs of the welding process itself, a plethora of variables conspire to either aggravate or ease the existence of porosity. In this extensive guide, we will certainly untangle the scientific research behind porosity, discovering its impacts on weld top quality and unveiling advanced techniques for its control. Join us on this trip through the microcosm of welding blemishes, where precision meets understanding in the search of remarkable welds.
Recognizing Porosity in Welding
FIRST SENTENCE:
Assessment of porosity in welding reveals vital insights into the honesty and quality of the weld joint. Porosity, defined by the visibility of tooth cavities or voids within the weld steel, is a common concern in welding procedures. These gaps, otherwise appropriately dealt with, can jeopardize the architectural stability and mechanical buildings of the weld, leading to possible failings in the finished product.
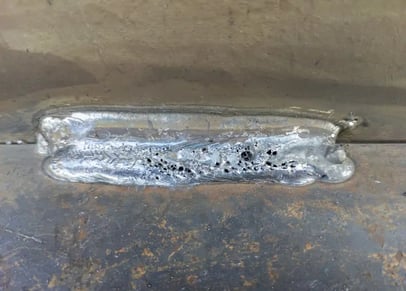
To identify and quantify porosity, non-destructive testing methods such as ultrasonic testing or X-ray evaluation are commonly used. These strategies enable the recognition of inner issues without endangering the honesty of the weld. By analyzing the size, shape, and distribution of porosity within a weld, welders can make informed decisions to enhance their welding processes and accomplish sounder weld joints.

Factors Affecting Porosity Development
The incident of porosity in welding is affected by a myriad of elements, varying from gas securing effectiveness to the ins and outs of welding parameter settings. Welding specifications, consisting of voltage, current, travel speed, and electrode kind, additionally impact porosity formation. The welding strategy employed, such as gas steel arc welding (GMAW) or secured metal arc welding (SMAW), can affect porosity development due to variations in warm circulation and gas coverage - What is Porosity.
Effects of Porosity on Weld High Quality
The visibility of porosity additionally deteriorates the weld's resistance to rust, as the trapped air or gases within the voids can respond with the surrounding setting, leading to deterioration over time. In addition, porosity can impede the weld's ability to withstand stress or influence, additional jeopardizing the total high quality and reliability of the bonded structure. In critical applications such as aerospace, vehicle, or structural buildings, where safety and toughness are critical, the harmful results of porosity on weld high quality can have severe repercussions, emphasizing the relevance of reducing porosity through correct welding techniques and treatments.
Methods to Minimize Porosity
To boost the quality of welded joints and make certain structural honesty, welders and Get More Information fabricators utilize certain techniques focused on lowering the formation of spaces and tooth cavities within the product throughout the welding procedure. One efficient approach to minimize porosity is to make sure proper material preparation. This consists of thorough cleaning of the base steel to remove any type of pollutants such as oil, oil, or wetness that can add to porosity formation. Additionally, making use of the suitable welding criteria, such as the correct voltage, present, and take a trip rate, is crucial in stopping porosity. Keeping a consistent arc length and angle throughout welding additionally aids decrease the probability of porosity.

In addition, picking the ideal shielding gas and keeping proper gas flow prices are vital in lessening porosity. Making use of the suitable welding strategy, such as back-stepping or employing a weaving activity, can additionally assist disperse warm uniformly and minimize the opportunities of porosity development. Finally, making sure appropriate air flow in the welding atmosphere to eliminate any type of potential resources of contamination is essential for accomplishing porosity-free welds. By carrying out these methods, welders can effectively decrease porosity and create premium welded joints.
Advanced Solutions for Porosity Control
Applying innovative modern technologies and ingenious approaches plays an essential function in attaining exceptional control over porosity in welding procedures. One sophisticated remedy is the usage of sophisticated gas mixes. Securing gases like helium or a blend of argon and hydrogen can help in reducing porosity by providing far better arc stability and boosted gas coverage. In addition, utilizing innovative welding methods such as pulsed MIG welding or modified ambience welding can also assist minimize porosity problems.
Another sophisticated solution includes the usage of advanced welding devices. Using devices with integrated features like waveform control and advanced power resources can improve weld top quality and minimize try this site porosity risks. The execution of automated welding systems with specific control over criteria can dramatically decrease porosity defects.
Additionally, integrating advanced monitoring and inspection technologies such as real-time X-ray imaging or automated ultrasonic screening can assist in identifying porosity early in the welding procedure, enabling immediate corrective actions. Overall, integrating these sophisticated solutions can significantly improve porosity control and enhance the total top quality of bonded elements.
Conclusion
Finally, view website comprehending the science behind porosity in welding is essential for welders and makers to create top quality welds. By identifying the variables affecting porosity development and applying strategies to minimize it, welders can boost the general weld high quality. Advanced solutions for porosity control can better boost the welding procedure and make sure a strong and reputable weld. It is essential for welders to continually educate themselves on porosity and apply best techniques to achieve optimum results.
Report this page